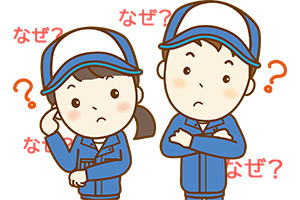
トヨタ生産方式でよく出てくる「なぜなぜ分析」があります。なぜなぜ分析は5回繰り返すことが推奨されているため、わかりやすく「5回のなぜ?」という名称でも呼ばれています。「5回のなぜ?」については、日頃現場改善に携わっている人はもちろん、オフィスでデスクワークを担当している人など多くの人が知っていることと思います。また「5回のなぜ?」を職場で実際に活用したことがある人も多いと思います。
しかし、実際に「5回のなぜ?」を生産ラインのトラブルなどで実際に使ってみると、意外にそう簡単なものではないなと思う人がほとんどではないでしょうか。
このコラムでは、生産現場における「5回のなぜ?」とは何か。「5回のなぜ?」の導入がそう簡単でない理由や、成功のコツを、事例を用いてご説明いたします。
そもそも「5回のなぜ?」とは
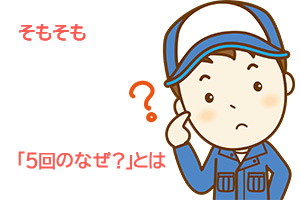
「5回のなぜ?」とは、問題や課題に対して、5回の「なぜ?」を繰り返し、その真因を探るための、トヨタ生産方式で用いられる手法です。
「火のないところに煙はたたない」というように、ものごとにはすべて原因があります。問題や課題にも原因があって起こっており、これを「原因結果の法則」と言いますが、「5回のなぜ?」のベースの考え方にこれがあります。したがって、問題や課題に対して、「なぜ?」を何度も繰り返して、原因を深く追求する必要が出てきます。
実際は、2~3回の「なぜ?」で済む場合もあれば、5回以上の「なぜ?」が必要な場合もあります。なぜを問う回数の「5回」というところが重要ということではありません。問題や課題の真因が分かるまで問い続けるということが大切なのです。その結果、対策方法もおのずとわかります。
この手法は、工場で品質などのトラブルが発生した場合に、同じことが二度と発生しないようにする、いわゆる「再発防止」のための手法として大変よく使われます。ISO審査でも、品質問題が発生した場合の再発防止策がしっかりできていないと厳しく指摘されることになるため、「5回のなぜ?」はたいへん有効です。
「5回のなぜ?」の活用にはコツが要る
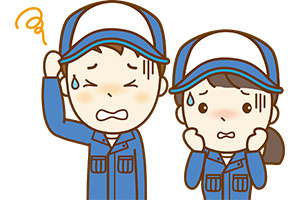
「5回のなぜ?」では、問題や課題の真の原因(真因)にたどり着くまで「なぜ?」を繰り返しますが、この部分でコツをつかまないとなかなか成果を出すことは、実際に難しいものなのです。
生半可な取り組み姿勢ではうまくいかないばかりか、「なぜ?」の原因追及がとんでもない方向へ行き、真因から大きく外れてしまうことや、藪の中に入りにっちもさっちもいかなくなることが実際よくあります。
そのためか、多くの中小企業で、生産ライン等の改善のご支援をさせていただいてきましたが、「5回のなぜ?」がしっかり定着している企業はほとんどありませんでした。「5回のなぜ?」は、手法そのものは実にシンプルなのですが、役立てるにはそれなりのコツが必要です。
零細企業の工場であれば、何か問題が発生すると、真因が追求されていなくても決裁権がある社長に相談すれば、強引に問題解決することが多いため、あまり「5回のなぜ?」を必要とされないことがあります。反対に、大企業であれば、「5回のなぜ?」が正しく活用されていることでしょう。ゆえに大企業にまで成長できたとも言えます。問題は中小企業です。
中小企業の場合は、現場のルールがバラバラなために、「5回のなぜ?」を行ったら、「真因は基本ルールを作っていない社長が悪い」という具合に責任のなすりつけ合いや個人攻撃におちいり、本来の真因から外れてしまうことが多々あります。
上司の責任になることはあっても、小さな会社はともかく、社長の責任は行き過ぎです。「5回のなぜ?」のコツは、自己責任として捉えることです。
「5回のなぜ?」は、製造現場においては、現象が起こったことに対しての原因追及と、不良品が流出してしまったことの原因追及をします。そのときに、自己責任としてどこに原因があったのかを追求することがコツです。
「5回のなぜ?」に取り組んで成功に導くコツをつかむために、まずは具体的な事例をとりあげながら、基本的なポイントを説明したいと思います。
「5回のなぜ?」の事例
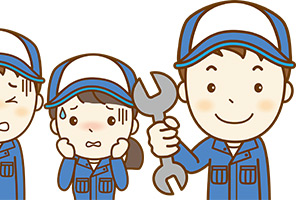
ここで取り上げる事例は、カンバン方式で有名な大野耐一氏が、名著『トヨタ生産方式』(ダイヤモンド社)で紹介されているものです。比較的分かり易い事例なので、『「5回のなぜ?」とは何か』を人に説明する際に、私流にアレンジしてよく使っているものです。
「工場のとある生産ラインで、金属加工のための加工設備(ミリングマシン)が使用中に停止した」という問題に対して、「5回のなぜ?」を行ってみたいと思います。この故障が原因で、大きな品質問題が発生してしまい、納入先から再発防止が強く要求されているという状況です。
1回目のなぜ?
まず、1回目の「なぜ?」です。なぜ、使用中の加工設備が停止してしまったのでしょうか。原因追及では、まずは三現主義に立ち返り、現地、現物、現実(現象)を五感で見ます。これについては、後ほどご紹介します。
さて、1回目の「なぜ?」では、「設備が停止した原因は、ドリルの回転軸に潤滑油が十分に流れていなかったので、過負荷のためヒューズが飛び、加工設備が停止してしまった」ということが、実際に調べることで確認できたとします。
2回目のなぜ?
1回目の「なぜ?」で導き出された原因に、2回目の「なぜ?」を行います。なぜ、ドリルの回転軸に潤滑油が十分に流れていなかったのでしょうか。
「ドリルの回転軸に潤滑油が十分に流れていなかった原因は、ドリルの回転軸に潤滑油を供給する、加工設備に付帯している油循環ポンプの回転軸が摩耗でガタガタになっているため、潤滑油を十分送り出せなかったためである」ということが確認できました。
3回目のなぜ?
3回目の「なぜ?」です。なぜ、油循環ポンプの回転軸が摩耗していたのでしょうか。
「油循環ポンプの回転軸が摩耗した原因は、油循環ポンプの軸受け部に、金属の切り屑が入って詰まったためである」ということが、油循環ポンプを分解して調べることで、確認できました。
4回目のなぜ?
4回目の「なぜ?」です。なぜ、循環ポンプの軸受け部に金属の切りくずが詰まったのでしょうか。
「金属の切り屑が、軸受け部に詰まったのは、潤滑油の中に含まれる切り屑を除去(ろ過)する、フィルターが破損して小さな穴が開いていたため、切り屑が通りぬけて軸受け部に入り、摩耗した」ことが、さらに調査することで確認できました。
5回目のなぜ?
5回目の「なぜ?」です。なぜ、フィルターに小さな穴が開いていたのでしょうか。
「フィルターに穴が開いたのは、フィルターの寿命を超えて使用したため」ということが確認できました。このあたりで、「加工設備の故障の(直接)原因は、油循環ポンプについているフィルターを更新していなかったことである、と結論をだしてもよいでしょう。したがって、対策としては、「新しいフィルターと交換する」ことであると言えます。
しかし、フィルターの寿命を超えて使用して、そのことに故障するまで気づいていなかったということは、何か仕組みに問題があるかもしれません。もし仕組みに問題があったとしたら、新しいフィルターへの交換は、暫定処置ということになります。
「5回のなぜ?」から導き出される再発防止策
さらに6回目の「なぜ?」をしてみたいと思います。なぜ、寿命を超えたフィルターを使用していたのでしょうか。
「フィルターの寿命を越して設備を使用していたのは、フィルターの更新のルールがなかったため」ということが確認できました。このレベルで「真因」に到達したと言えるでしょう。
再発防止としての恒久対策は、「更新必要時期を調査確認し、更新時期にはフィルターを確実に更新する」とルールで決めることです。例えば、自動車の車検時期のように、フィルターを新品に更新するときに、「次の更新必要な時期を、設備のそばに明示しておくこと」などが考えられます。
もちろん、加工設備を使用するスタッフに、フィルター更新についての教育訓練をしておくことも必須です。さらには、設備保全担当部署では、点検や更新を忘れないでタイムリーに実施するために年間の保全計画(私は「保全カレンダー」と呼んでいます)を作成しますが、その保全計画の中に、フィルター更新時期を忘れないように計画に入れて置くことで再発防止がより確実になります。
これらの恒久対策により、設備の故障頻度が軽減し、品質が向上し、稼働率が向上することで、「仕事の成果」につながるのです。
この事例では、6回目の「なぜ?」で、やっと原因に到達し、恒久対策を打つことができました。この事例には多くの大切なポイントが組み込まれていますので、よく理解し納得され、「5回のなぜ?」を実際に現場で活用していく中で、コツを体得していただけることと思います。
「5回のなぜ?」で真因をつかむためのマインドとスキル
ここで皆さんが職場で「5回のなぜ?」を実践する際に、藪の中に入ることなく真因をつかみ適切な対策をすることができるようになるためには、「5回のなぜ?」に取り組む「マインド」と「スキル」にポイントがあります。
以下、臨む姿勢や習慣、態度、心構えなどのマインド面を2つのポイントから、必要な知識や思考方法、テクニックなどのスキル面を6つのステップから、上述した事例の一連の流れに沿って順次説明していきたいと思います。
「5回のなぜ?」を成功に導くための2つのマインド
ポイント1、探求マインド
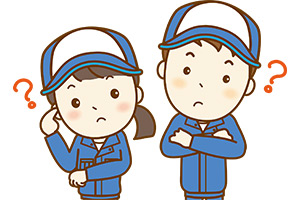
製造業改善コンサルタントとして、実際に現場で「5回のなぜ?」に取り組む方の活動を見ていてまず思うことがあります。それは、真因に至ってなくても、満足して終了してしまうケースが大変多いということです。
例えば、この事例で2回目の「なぜ?」で終わっていたとしたら、「原因は、軸受け部がガタガタに摩耗したためであるから、対策は、新品の軸に交換することである」ということになってしまいます。これでは、軸受けを新品に交換しても、やがてすぐに、同じような問題が再発することが容易に理解できるでしょう。
また4回目の「なぜ?」で終了し、対策として新しいフィルターと交換しても、またフィルターの交換を忘れ、やはりトラブルが再発します。
要するに、「真因が得られた」と納得できるまでは、「なぜ?」を繰り返さなければなりません。「納得できるまで」と述べましたが、姿勢として「導き出された真因への対策をきちっとすれば、問題は絶対に再発しない!」と本心から思えるかということです。「同じ問題が起こりえないか?」「他の原因はないか?」をもう少し考え、謙虚に冷静にチェックしてみればわかります。
問題や課題を見える化し、仲間と共有化して一緒に確認することで、より確実になるかもしれません。ただ、「5回のなぜ?」に取り組む姿勢が間違っていたら、複数人数いてもムダになります。
ポイント2、協働マインド
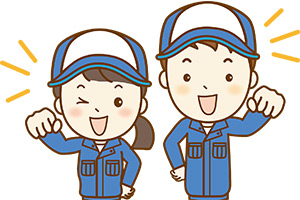
2つ目のポイントとして、自分の担当外の他の工程でトラブルが生じた場合の対応です。自分の担当外の工程でのトラブルでも、自分の仲間がトラブルに遭遇しています。「5回のなぜ?」を実施する人は、同じ職場で生じた問題に対しては、傍観者ではなく当事者意識をもち、「すべては自分の責任である」という心構えがもてることです。もし自分が事前に問題を把握できていて、その人にアドバイスできていれば、トラブルは未然に抑えられていたはずです。
こういった心構えが当たり前になっている職場では、「この問題は、誰かが上司に報告しているだろう」「あの人は、この問題を把握しているに違いない」というポテンヒットはまず起きないでしょう。皆で協働して問題をカバーし合うからです。こういったマインドが浸透している職場では、再発不良はまず生じないし、品質や生産性も継続的に向上し、より多くの利益がだせる、最強の職場になることは間違いないと言えます。
「5回のなぜ?」を成功に導く6つのスキル
最初に、「5回のなぜ?」で、「真因に確実にたどり着くまでにはコツが必要だ」と述べました。これは、「なぜ?」を繰り返すうちに、とんでもない方向や藪にはいってしまうことを防ぐためのコツです。
以下、「5回のなぜ」の流れに沿い、6つのステップを取り上げます。この6つのステップにおける大切なことを、私の現場体験や知識などから集約し綜合したスキルです。
ステップ1、目的やリソースの明確化
「5回のなぜ?」は、対象のトラブルを解決し、「その結果どうしたいのか」「どうなりたいのか」といった、目的や落としどころを明確にしておくことが大切です。単に上司や仲間から頼まれたという理由で、目的も理解・納得もしていないまま「5回のなぜ?」にとりかかってはいけません。疑問があれば、現場の当事者に必ず直接聞いて確認すべきです。さらに落としどころの要件として、問題解決の期日や必要時間、必要な費用などを確認しておくことも欠かせません。
ステップ2、現地・現物・現実(現象)の三現主義
「5回のなぜ?」は、現場改善をすることが目的ですので、当然ですが、少なくとも最初は会議室や別の場所でなく、必ず現場へ行き、自ら問題点を確認する「三現主義」が前提です。
その際は、不要な先入感を持たず、ありのままを自分の五感を通じ観察することです。観察の仕方についてはコラム「見える化とは」をご参照ください。現場を確認しても問題点が把握しきれない場合は、現場の当事者から背景を聞いたり、必要な情報を得たりすることも大切です。
いずれにせよ、このステップでは、三現主義に基づいて現象面を把握し、対象とする問題点を、明確に理解し自分事として納得することです。
もし三現主義に基づかないで、机上だけで原因を考えていたら、「ヒューズが飛んだ原因が漏電に違いない」と判断して、電気系統ばかりを調査することになりかねません。
ステップ3、5ゲン主義(現地・現物・現実+原理・原則)
いよいよ「5回のなぜ?」のはじまりです。五感をフルに活用しながら、何が原因なのか、観察し、必要な調査をします。
その際、右脳思考(感性主体)と左脳思考(論理=原理・原則主体)の両方が必要です。違和感がありしっくりしない場合は、原理・原則に照らし合わせ、違和感の原因をチェックします。また現象があまりに複雑であり、因果関係が把握できそうもない場合は、感性や直観に頼ることで大きな間違いは防げます。
ステップ4、仮説と検証(科学的アプローチ)
「仮説と検証」という言葉は、コンビニ大手の「セブンイレブン」ではアルバイトの従業員でも使っていることで有名になりました。「天気予報で『午前晴れ、午後より雨』といっていることから、午前から出かける人はおそらく傘をもっていない人もいるので、午後雨が降り始めれば傘を買う人は何人かいるだろう」というのが仮説にあたります。実際に「午後から雨が降ったらすぐに傘を店頭に並べる」ことで実際に売れるかどうか、仮説が正しいかどうかが「検証」できることになります。
さて、上述の故障事例の中で言えば、2回目の「なぜ?」では、「油循環ポンプが何らかの原因で機能不全になり、ドリルの回転軸に油が流れなくなった」というのが仮説にあたります。それを検証する目的をもって、循環ポンプを分解し、詳細を観察し、右脳・左脳を駆使することで、機能不全の原因が循環ポンプに付着する金属の切り屑が正体であることが発見できたわけです。
もし仮説をもたず、やみくもにカンコツだけで設備を分解したりしては、生産がストップする時間がムダになるばかりか、原因究明のノウハウが共有できない恐れがあります。もし仮説が間違っていたとしても、次に可能性の高い仮説を取り上げて検証すればよいだけのことです。仮説と検証の科学的アプローチを行えば、決して藪に入ったりすることはありません。
ステップ5、目的の達成可否
問題や課題の真因が分かれば、対策案がいくつか出てくるはずです。「ステップ1の目的が達成できるか」「要件としての期日や費用は満足できるか」をチェックし、適切な対策を選んで実行します。実際に目的が達成でき、しかも要件も満足できれば、「5回のなぜ?」が成功したことになります。
ステップ6、報告・共有
「5回のなぜ?」を行った後は共通フォーマットのシートにまとめて報告し、関係者で共有することが大切です。それをミーティングで発表するなどして、一人で得られたノウハウを全員で共有することができます。この繰り返しで、現場でのトラブルが大幅に軽減されます。
5S改善七つ道具「なぜなぜシート」
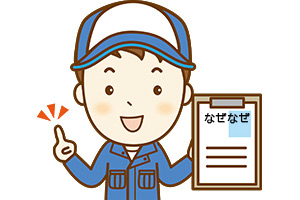
ここまで読まれた皆さんは、「5回のなぜ?」の全体像が見えてきたことと思いますし、成功するためのポイントも理解されてきたと確信します。
あと必要なことは、職場での5S改善活動で「5回のなぜ?」を実際に使ってみることです。私の経験からも言えるのですが、理屈だけではなく最後は実践です。
コラム「見える化とは」でも書きましたが、製造業改善コンサルティングで用いる「5S改善の七つ道具」の中に、「5回のなぜ?」を行うための「なぜなぜシート」というものがあります。このシートは多くの企業で使い、シンプルなツールに磨き上げてきたものです。5S改善活動の仕組みの中に、この「なぜなぜシート」というツールが仕掛けとして組み込まれています。
「5回のなぜ?」において、この「なぜなぜシート」を5S活動で活用しつづけ、改善ミーティングで共有することで、皆さんの職場で「5回のなぜ?」が必ず定着し、ますます成果をだしていくことができることを確信しております。
最後に
以上、「5回のなぜ?」のやり方やマインドについて述べましたが、話を聞いただけでは、真因を見抜くことが難しいため、現場に定着させることは困難な場合があります。その場合は、製造業改善コンサルティングをご依頼ください。5S活動の一環として、「なぜなぜシート」を用いた「5回のなぜ?」のやり方やマインド、改善ミーティングのやり方、改善実施の方法を、徹底的にご指導いたします。
「5回のなぜ?」の導入や定着化を行って、現場でのトラブルを軽減し、生産効率を高めたいなら、ぜひ製造業改善コンサルティングの導入をご検討ください。
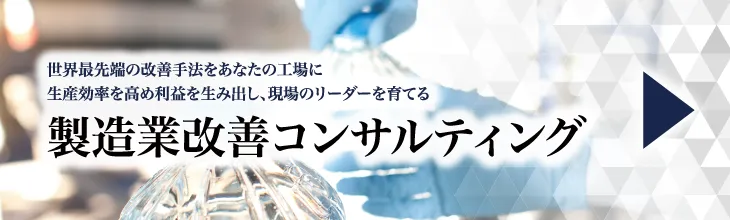