製造業改善コンサルティング
5S活動の導入・定着化
5S活動の導入・定着化は、製造業改善コンサルティングの標準プランの内容の一つです。5S活動では、5S改善体制づくりで把握した真の問題点を改善すべく、各種ツール開発や見える化を行い、改善活動を定着化させます。5S活動を行うと、QCDなどが改善され、製品の製造やサービス提供のリードタイムが大幅に短縮できます。リードタイムが30%程度低減することは、当たり前のように起こります。
5S活動の効果
5S活動の導入・定着化は、5S改善体制づくりの後に実施いたします。これらにより次のような効果が得られます。
- 製品製造やサービス提供のリードタイムが短縮できる(目標30%以上短縮)
- 現場がすっきりして、作業環境がよくなり、事故の数が減る
- 品質が改善され、原因不明の慢性不良やクレームが減る
- 設備故障が減り、メンテナンス費用の軽減や生産性が向上する
- 生産に追われてバタバタすることが減る
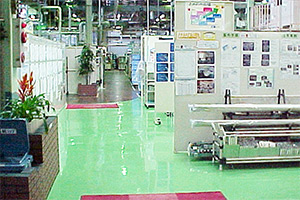
この写真は、ショールームではありません。とある自動車部品メーカーの工場内を入口から撮影したものです。長年の5S活動でピカピカの工場を実現しました。
5S活動が徹底され、通路の一番奥まで床が光っていることがわかります。20m先に、油のシミやネジが落ちていても気が付くほどです。
綺麗な工場なので、工場の見学者が増えたこともあり、従業員の休憩やコミュニケーションができる場所を兼ねて、工場の入り口に来客用ブースを設置しました。
工場内で働く従業員は、「自分たちがつくり上げた美しい工場をもっと知ってもらいたい」と、高いモチベーションで仕事に取り組むようになりました。
村上式製造業改善コンサルティングの5S活動では、極力費用をかけず、従業員にもムリなく、このような美しい工場を目指すカルチャーをつくり上げます。
5S活動の流れ
5S改善体制づくりと5S活動(月2回、3か月程度)
責任者・部門長・グループリーダーへの個別ヒアリングを順次実施し、真の問題点を本音ベースで把握します。ヒアリング内容は、匿名で社長に報告いたします。工場が複数ある場合には、まずは会社を代表する工場からはじめます。
現状把握と並行し、コンサルタントが指導しながら、責任者が5Sチェックシート作成、5S活動ルール作成、改善ミーティング実施ルール作成、改善提案制度等の学習やしくみづくり等を行います。
5Sチェックシートや改善計画表のテンプレートやその他必要な資料は、コンサルタントがご用意いたします。貴社ですでに資料があったとしても、時代に即した当社オリジナル資料を用いてコンサルタントと共に作り直していただきます。
なお、5S体制づくりの期間でも、必要な環境整備や設備故障等の問題に対しては、コンサルタントの指導のもと、すぐにできる改善は即実施していただきます。
5Sチェック実施(基本月2回)
5S活動体制ができたら、5Sチェックシートを用いて責任者とグループリーダーが5Sチェックを、自主的に随時行っていただきます。コンサルタントが同行してのチェックは、月2回を原則とします。
改善計画表の作成と掲示
5Sチェック時の指摘事項の原因と対策についてはグループリーダーを交えて打ち合わせし、改善実施の責任者や決裁者は誰なのか、問題点とその原因と対策、誰がいつまでに改善するか決め、改善計画表に記入します。
問題の真因が判らない場合は、改善ミーティングで「5回のなぜ」を実施します。
責任者が5Sチェックシートと改善計画表を工場に張り出し、それらの写しを社長に提出します。この工程は班ごとにグループリーダーが自主的に行います。
改善ミーティング
改善ミーティングは5Sの問題点について話し合い、知恵を出す場です。グループリーダーが中心となって、班ごとに月2回(各30分程度)行います。改善ミーティングで出された5S活動のアイデアは、重要度と緊急度で分類し、実施順序を決めて取り組みます。
当初は月2回程度、プロジェクト責任者とグループリーダーの指導を行います。改善計画表に基づいて改善指導やコンサルティング等を行いながら工場の改善を行っていただき、定着化させます。
また、グループリーダーは「PDCA報告シート」を月1回プロジェクト責任者に提出し、プロジェクト責任者はグループリーダーに指示を出します。3ヶ月に1回、3ヶ月分のPDCA報告シートを社長とコンサルタントに報告します。
発表会実施
年1回の発表会では、グループ毎に5S活動の成果と次年度の計画を、グループリーダーが発表します。その後、改善提案制度に基づいて貢献した人を、社長に表彰していただきます。
初回の発表会は、5S活動を開始してから1年後に行います。
5S活動の年スケジュール
1年目、チェンジ
目標として、品質問題や設備トラブルなどの不安やバタバタした職場環境とは決別しなくてはなりません。そのためには今までの意識をチェンジ(変革)し、各人が主人公として責任を再度確認することが必須と思われます。改善体制づくりと同時に、各グループ内でも、5S改善の七つ道具や改善ミーティングをフルに活用し、徹底的に5Mベース(加工設備、部材、作業マニュアル等)で環境整備をすすめていきます。
2年目、チームワーク
グループリーダーの役割は、グループ内のチームワーク構築・強化にとどまりません。グループリーダーが他のグループのラインを5Sチェックし合い、グループリーダー交流会で意見交換を行う、グループリーダー交流会を実施します。それにより、自分のグループの客観的な評価や他のグループの取り組みから気づきが得られ、グループ間でのアイデアの出し合いの良い競争が起こり、各グループに活気が出ます。
さらには、チームワークを促進するため、改善ミーティングを浸透定着させます。
3年目、チャレンジ
個人のチャレンジは勿論、グループとしてチームワークを発揮し、限界にチャレンジし、他のグループとも改善を競い合います。3年目には改善提案制度に表彰制度が導入され、個人やグループとしての優れた成果は表彰され称えられます。また、リーダー体験発表やスキルアップの認定制度を導入し、個人の成果、スキルやマインドの成長を評価し称えます。そのため、各人に働きがいが得られ、工場全体の利益創出につながり、工場全体が美しく光り輝きます。