製造業改善コンサルティングは、ご契約の前に無料で「簡易5S診断」を行っています。この簡易5S診断を行うだけで、生産性を10%程度高めることができます。なぜ簡易5S診断を実施するだけで生産性が高まるのかの理由を、そして、簡易5S診断で生産性を高めるための方法をまとめました。
なぜ簡易5S診断だけで生産性が高まるのか?
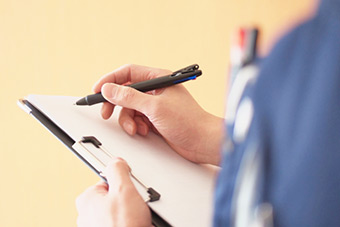
5S活動は、特別なスキルやノウハウは全く必要なく、その気にさえなれば、素人でもやれるという特色があります。改善効果がすぐ出て達成感も得られます。5Sの内容は、自宅の整理整頓と本質的に同じです。
5S活動に必要となるマインド(意識)は、「他人に不快な思いをさせたくない、少しでも喜んでもらいたい」という他人への思いやりです。このマインドは、だれも否定できるものではありません。
5Sとは単に「きれいにすること」と考える人が多々いますが、これだけでは生産性は高まりません。5S活動の基本は「整理・整頓(2S)」です。整理とは、不要なものを捨てること。整頓とは、必要なものをいつでも取り出し、使える状態にすることです。これらを正しく理解し実行すれば生産性が向上します。
トヨタ生産方式には「七つのムダ」ということばがあります。生産工場で発生するムダを、顧客にとって何ら価値を生まない(お金は請求できない)仕事を七つに分類することができるということです。
7種類あるムダな仕事(時間)は、通常の生産工場では、作業時間全体の60%~80%以下に下げることは難しく、トヨタといった一流とされている会社でも50%は下らないと言われています。この数値は、私の体験からも十分納得できます。
ある生産工場では、部材置き場の整理・整頓(2S)が悪く、雑然とものが置かれ積み重なっているだけで、ものの表示は全くなく、先入れ先出しももちろんできていない状態でした。ものを探し出し、奥から取り出し、台車に積み、自分の生産セルに戻るという作業時間が、その人の作業時間全体の70%以上を占めて、それ以下に下らない状態でした。
要は、「現場は宝の山」であり、5S活動で改善できることは山ほどあるということです。「その気になれば、10%の生産性は即向上する」というのは、伊達や酔狂で言っているのではありません。
簡易5S診断の内容
簡易5S診断では、コンサルタントが、社長や工場長など現場状況を説明できる方にご同行いただき、5Sチェックシートを使い、5S活動のレベルを簡易評価いたします。(約2時間)
簡易5S診断の評価項目
評価項目は、次の3点の進化軸の組み合わせ(ポートフォリオ)となっています。
- 「ものの5S」(ものの整理整頓ができているか、ものの表示はできているか)
- 「設備の5S」(設備がいつでも使えるよう管理状態にあるか)
- 「仕事の5S」(5S活動に必要な仕事のPDCAが回っているか、見える化されているか)
基本的な評価対象エリアは、工場外(駐車場・工場建屋周り)、エントランスや事務室、オフィス、応接室・トイレはもとより、工場内では、通路や部材置き場から生産ライン、出荷倉庫まで、顧客から見える部分のみではなく、顧客から見えにくい設備の裏側や倉庫の隅なども評価します。
ただ、時間が2時間程度に限定されているので、工場の規模にもよりますが、とくにご希望がない限り、改善効果が出やすい生産現場に対象を絞り注力いたします。
簡易5S診断の採点方法
5Sチェックシートでの採点方法は、20項目を5段階評価(「1点」:全くダメ、「2点」:少しだけ、「3点」:普通、「4点」:もう少しで、「5点」:完璧)いたします。これは、過去種々の評価方法を現場で試してきましたが、すぐに誰もが使え、人による差も出にくく、組織で共有化しやすい内容ですので、評価後すぐさま貴社の社内で共有化できます。
現場での診断終了後、評価結果や問題点、課題などのご指摘とその理由をご説明いたします。
製造業改善コンサルティングを正式にご契約される場合は、初回キックオフ(契約後1ケ月ほど)にて、責任者とグループリーダー全員で現場を回り、簡易5S診断での指摘事項の改善状況を確認いたします。改善意欲がわかり、コンサルティング導入後の伸びしろや将来性もみえてきます。
簡易5S診断で効果的に生産性を高める方法
簡易5S診断で効果的に生産性を高めるために、簡易5S診断当日に行われる事前打合せにて、コンサルタントから、打ち合わせ参加者(社長、工場長、責任者他)に対し、5S活動の目的、意義、取り組み姿勢、および診断の方法や5Sチェックシートの説明を行います。また、現場での5S診断終了後の打合せにて、気づいた点や問題点をご指摘いたします。併せ、効果的に改善を進めるためのマインド(意識変革)や実施方法について、主に以下のポイントについてご説明いたします。
5Sに対するマインド(意識変革)
工場は単に商品を製造するだけでなく、お客様にとってショーウインドウです。お客様を工場案内することは、工場をPRすることです。お客様に、日々の改善への取り組み姿勢といった、お客様からは直接には目に見えにくい競争力、QCDの実力を知っていただくことで、信頼感が醸成され強い絆ができ、益々の商売につながります。また、マーケティングや営業の絶好の機会にもなります。
5S活動の実施は、従来の生産活動の単なる延長ではなく、「新たに5S活動にとりくみ成果を出していくんだ」という覚悟が必要です。この点では、社長の強いリーダーシップが必須であり、それによって5S活動の効果が変動します。
5S活動の最終ゴールは、「目標を全員で共有し、チームワークを発揮し、目標達成に一人一人がチャレンジすること」で、業績として成果を出しつつ、全員が成長しつづけることのできる働きがいのある美しい工場の構築にあります。短期の成果のみにとらわれ焦らず、長期の視点を忘れないように肝に銘じることが大切です。
効果的な5S活動の方法
短期決戦で、早い段階での成功体験を確実に得るために、簡易5S診断でご指摘した問題点に対して、グループや担当者レベルで実行責任を明確化します。また、社長や工場長、責任者も、問題を部下に丸投げするのではなく、状況をフォローしたり実行を見届けたりして、しっかり関与することにより成果は大きく変わります。ただし、経営幹部は、現場の具体的な細かな指示(マイクロマネジメント)は避けていただき、従業員の自ら取り組む姿勢を伸ばし、モチベーションを高めるように努めます。
5S活動は、まず簡易5S診断結果の評価点「1」(全くダメ)に着目します。特別な理由のない限り、評価「2」以上に上がることを目指してください。製造コンサルタントによる評価は、「絶対レベルよりも、どれだけ改善し、評価点が向上したか」、に注力いたします。ちなみに当面のゴールはすべての項目で評価を「5」にすることです。当面のゴールが達成されたら、評価項目を入れ替え、新たなゴールへとレベルアップします。
5S活動の導入が充分ではない工場では、たいてい余分なものが部材置き場や仕掛品置き場を占拠しております。まず、これらの「整理」(不要なものは捨てる)に集中し、徹底的にこだわることが成果を出すコツです。
不要品の仮置き場を工場の一画に設け、廃却日(業者引き取り日など)を決めます。廃却日前までに、捨てられては困るものがある方は、廃却前に自分の目で直接確認してください。
整理のルールでは、期日がきたら容赦なく廃却しても、あとで担当責任者にクレームをつけることはできません。廃却後は、全員で掃除をすることで、気分がスッキリします。このやり方で、過去、種々の工場で実践してきましたが、活動の早期にたとえ小さくても成功体験ができるので、大いに達成感が得られ、その後の活動に弾みがつきます。改善プロジェクトとしての大成功につながります。
キックオフでコンサルタントの審査を行わない場合は、社長や責任者で責任をもって同一の5Sチェックシートで評価していただき、どれだけ改善されたかを、後日コンサルタントにご報告ください。
この記事の著者
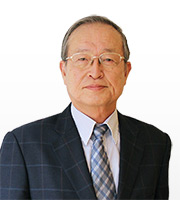
製造業改善コンサルタント
村上 豊 (Murakami Yutaka)
名古屋大学工学部、修士課程卒業後、トヨタ系列の電装を担う大手メーカーに30年間従事。製造部門のみならず、国内工場の工場長や英国の新工場立ち上げをも担当する。コンサルタントとして独立後、さまざまな製造業種の企業を支援し、5S活動の理論に基づいて工場の人材育成、生産、保全、品質、製造技術の改革に取り組む。人の能力を引き出し高めるマネジメントで、多くの製造工場の改善・改革、カルチャーづくり、理念経営を支援。