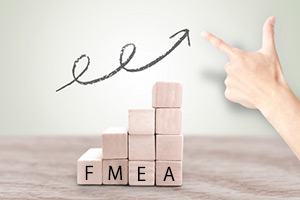
本コラムは、先のコラム「FMEAとは」の続編で、FMEAを実施して作成手順についての実践的解説版です。
まだ先のコラムをご欄になっていない方、とくに、FMEAを経験されている方も是非ご覧になられることをお勧めいたします。2019年6月に、FMEAが改定されているからです。
次の目次に沿って、FMEAのやり方を述べますが、最初に「FMEAの改訂の経緯」について、簡単に述べさせていただきます。
FMEAの改定について
従来日本で普及してきた「AIAG・FMEAマニュアル(米国)」は、長い間、自動車産業におけるFMEAのスタンダード的存在でした。しかし、近年の自動車産業を取り巻く環境変化には大変厳しいものがあります。顧客からの品質や安全に対する要求が厳しくなってきているからです。その流れは、自動車産業のみならず、各種製造や食品製造にまで及んできています。
その対応策として、上述の「AIAG・FMEAマニュアル(米国)」と「VDA・FMEAマニュアル(ドイツ)」は、「AIAG&VDA・FMEAハンドブック」として一本化されました。
主な変更点については、本コラムの中で、都度必要に応じてご紹介させていただきたいと思います。
FMEA作成手順
工業製品におけるFMEAには「設計FMEA(D-FMEA)」と「工程FMEA(P-FMEA)」があります。基本的にはこの2つが、FMEAの2本柱です。ただ、今回の改定で、「設計FMEA」を補完するものとして、「FMEA-MSR」(監視およびシステム応答の補足FMEA)が追加されました。これは、車載用の電気電子システム(カーナビ等)が対象になります。
「設計FMEA」や「工程FMEA」の作成手順は、共通の「7つの手順」を踏みます。
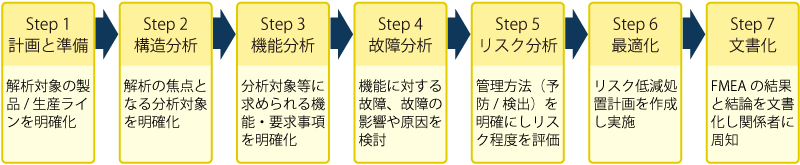
以下、この流れにそって、「設計FMEA」の作成手順を、次に「工程FMEA」の作成手順について、詳細にご説明していきます。なお、どちらの作成作業中にも、次の図のような、評価スコアや所要事項を記入できる「FMEAフォーマット」を用意しておき、これに記入していきます。
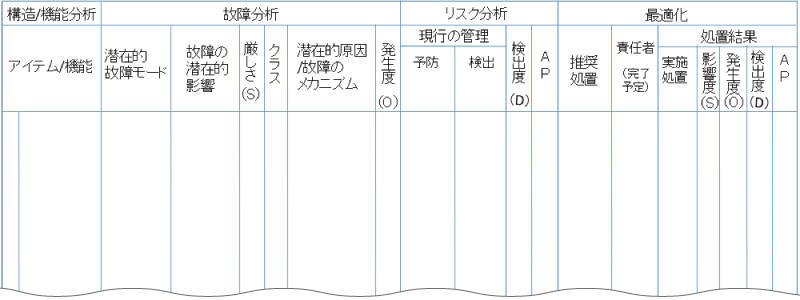
ちなみに、このFMEAフォーマットは、当社が行っているFMEAセミナーでサンプルとしてお配りしているものです。
FMEA作成準備
FMEAを作成していくために、設計/工程FMEA評価基準と設計/工程FMEA・処置優先度表(AP表)を用意します。
設計/工程FMEA評価基準
FMEA評価基準は、後ほどに詳しく述べますが、FMEAフォーマットにはFMEA評価基準を用いてランクを記入します。FMEA評価基準には、設計FMEAと工程FMEAでそれぞれ次の3種類(合計6種類)があります。
- 厳しさ(S)評価基準
- 発生度(O)評価基準
- 検出度(D)評価基準
設計FMEA評価基準の例
次の図は、設計FMEA評価基準の例です。右下からぞれぞれ、厳しさ(S)評価基準、発生度(O)評価基準、検出度(D)評価基準です。
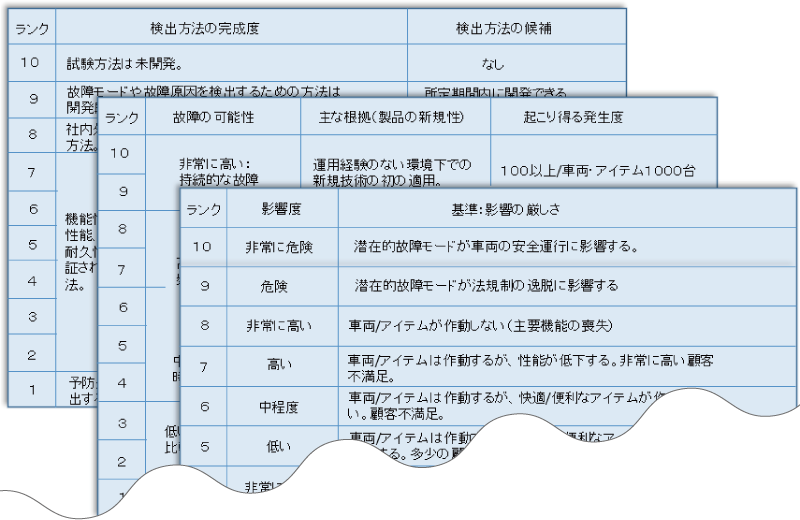
工程FMEA評価基準の例
次の図は、工程FMEA評価基準の例です。右下からぞれぞれ、厳しさ(S)評価基準、発生度(O)評価基準、検出度(D)評価基準です。
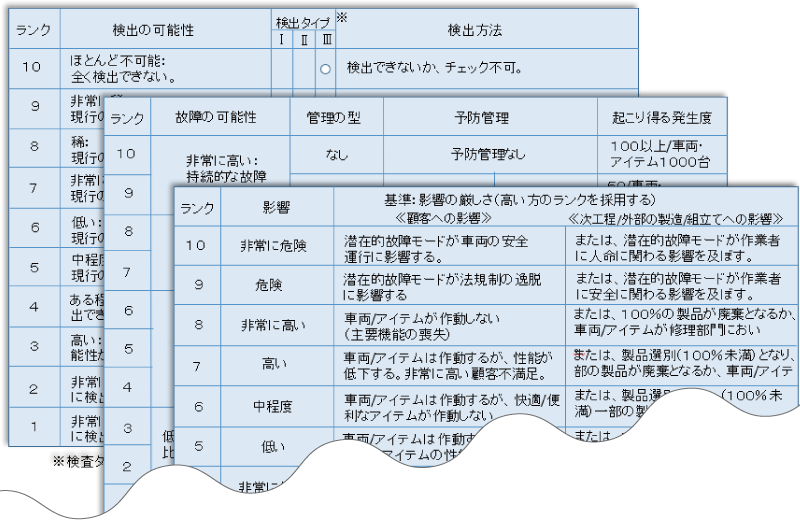
それぞれの評価基準は、故障モードが与える影響の度合いを10段階でランク付けする相対表です。例えば、故障モードが人身事故のような重大な事故の場合には、10ランクと定義します。
自動車業界のようにFMEAを当たり前のように導入している業界であれば、FMEA評価基準の内容が具体的に決められています。評価基準が創られていない業界の場合は、FMEAを作る前に、個々の企業オリジナルでFMEA評価基準を作る必要があります。FMEA評価基準の作り方は、中毒や病気、人身事故、故障などの業界のクレーム状況を集め、その重大性を10段階でランク付けします。
設計/工程FMEA・処置優先度表(AP表)
処置優先度(AP)も後ほど詳しく述べますが、FMEAの作成を進めていく中で、各故障モードに対して、それぞれ検出度(D)、発生度(O)、厳しさ(S)がランク付けさます。これらの兼ね合いによって、処置の優先度を決めなければいけません。
例えば、とある故障モードの厳しさ(S)が重大事故につながるとして、ランク10であったとします。その発生度(O)や検出度(D)がある程度のランクであれば、それは優先的に処置しなければなりません。
そのような優先度を決める基準のことを、処置優先度(AP)と呼び、H:High(高)、M:Medium(中)、L:Low(低)の3段階で定義した基準表を、FMEAの作成に入る前に用意します。
次の図は、設計/工程FMEA・処置優先度表(AP表)の例です。
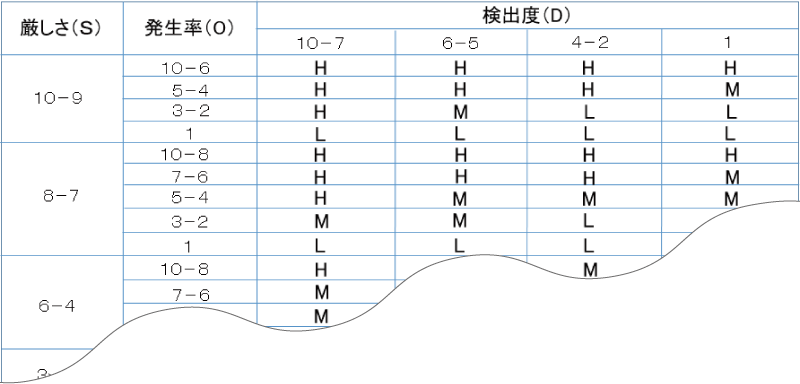
「設計FMEA」作成手順
FMEAには、設計FMEAと工程FMEAがありますが、先に設計FMEAのやり方をご説明いたします。実施例として、自転車の開発を想定しました。
手順1.計画と準備
FMEA解析の対象の製品及びその生産ラインの、システムやサブシステム、コンポーネントを具体的に明確にします。
例えば、貴社が「自転車(システム)」のサブシステムである「フレーム組立品」の開発計画中としましょう。フレームの組立にはいくつかの部品を用います。
次の図表「構造分析」をご覧ください。この場合、FMEA解析の対象は「自転車」全体となります。設計FMEAの上位には自転車というシステムがあり、下位にはフレームを構成するコンポーネント(部品)が6つあります。
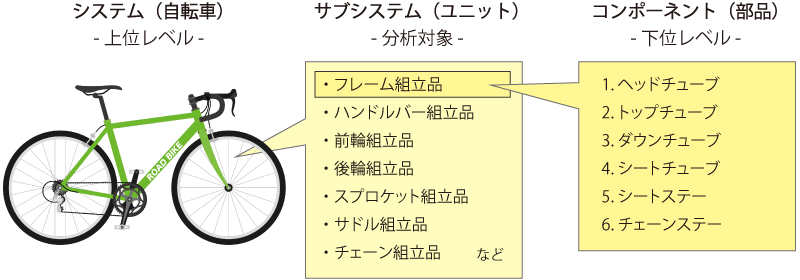
手順2.構造分析
FMEA解析の焦点となる「分析対象」の構造を明確にします。
ここで言う「構造」とは、上述の例では、「システム(自転車)」、「サブシステム(ユニット)」、「コンポーネント(部品)」の関連状態を示すものです。自転車のサブシステム(ユニット)である「フレーム組立品」を開発計画中なので、「フレーム組立品」が、FMEAの分析対象となります。
さらに、「フレーム組立品」は、6つのコンポーネント(部品)から構成されます。このように、「上位レベル」、「分析対象」、「下位レベル」の関係を明確にすることが、構造分析です。FMEA解析を着実に進めていくための、最初の大切なStepとなります。
この分析対象の「フレーム組立品」を、上述のFMEAフォーマットの「アイテム/機能」欄に記入します。
手順3.機能分析
分析対象(フレーム組立品)、システム(自転車)、コンポーネント(部品)それぞれに対し、求められる機能や顧客などからの要求事項を明確にします。次の図表、設計FMEA「機能分析・故障分析」をご覧下さい。
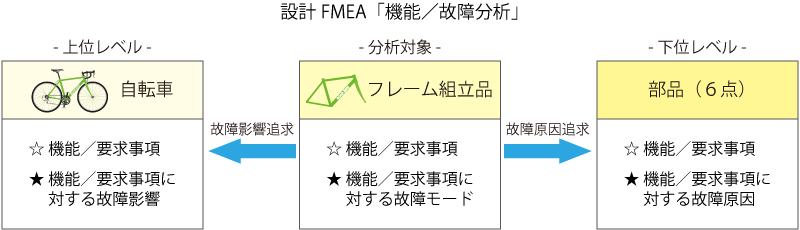
先にご紹介しましたFMEAフォーマットではスペースが限られますので、次の図表、設計FMEA「機能分析・故障分析」のようなイメージで、別途フォーマットを用意されることを推奨します。FMEAフォーマットと区別し、当社では「要求機能フォーマット」と呼んでいます。
分析対象の「フレーム組立品」、上位レベルの「自転車」、下位レベルの「部品(6点)」に対応させて、機能や要求事項を、要求機能フォーマットに記入します(図表中、☆印)。
手順4.故障分析
4-1 潜在的故障モードの検討
手順3で明確にした分析対象に対して、どのような故障モード(故障内容)が起こる可能性があるか、潜在的な故障を検討します。故障モードには、意図した機能を満たさないこと、顧客などからの要求事項を満たさないこと(不適合)の2種類あります。
分析対象の「フレーム組立品」に、故障モードを考えられる限り列記します。図表、設計FMEA「機能/故障分析」の分析対象の★印のところです。
最終結果をFMEAフォーマットの「潜在的故障モード」欄に記入します。
故障モードの例
製品の変形、緩み、漏れ、噛み込み、錆、不適切な信号、信号の断絶、電圧変動、力率の悪化など
4-2 故障の潜在的影響の検討
次に、リストアップされた潜在的故障モードが起こった時に、上位レベル(自転車)にはどのような影響があるか(故障影響)、顧客や使用者が気づく影響や安全の問題、法規制の逸脱などをリストアップし、要求機能フォーマットに記入します。図表、設計FMEA「機能/故障分析」の上位レベルの★印のところです。
最終結果をFMEAフォーマットの「故障の潜在的影響」欄に記入します。
故障の潜在的影響の例
製品の騒音、粗雑、誤作動、断続動作、不安定、臭い、漏れ、外観不良、環境への影響など
4-3 起こりうるトラブルの厳しさ(S:Severity)の評価
リストアップされた「故障の潜在的影響」を、「設計FMEA・厳しさ(S)評価基準」に基づいて10段階でランク付けします。厳しさ(S)のランクがもっとも高いもの、つまり起こりうる故障モードの影響の厳しさが高いものには10が付けられます。その反対に、ランクがもっとも低いものには1が付けられます。
これと同時に、製品の安全性に対する問題や、法規制の逸脱がないかを確認します。FMEAフォーマットにランクを記入します。
4-4 厳しさ(S)評価ランクのクラス分け
厳しさ(S)に付けられたランクが、9や10といった高いランクの場合は、工程FMEAチーム等への注意喚起をする必要があります。そのための「影響のクラス分け」を行い、設計変更によってランクを下げられるかどうかを検討します。
クラス分けのランクは、例えば以下のようにします。
クラスA | 影響度(S)=9、10 |
---|---|
クラスB | 影響度(S)=5~8、発生度(O)=4~10 (発生度については後程説明します) |
クラスC | 影響度(S)=1~4 |
クラス分けの結果をFMEAフォーマットに記入します。
4-5 潜在的原因/故障のメカニズムの検討
次に、下位レベルにおける故障モードの潜在的原因やメカニズムを検討します。
図表、設計FMEA「機能・故障分析」をご覧ください。下位レベルの部品に対し、想定される故障の原因やメカニズムを追求します。なお、1つの故障モードに対して、すべての潜在的原因及びメカニズムを検討し、要求機能フォーマットに列記します。図表、設計FMEA「機能/故障分析」の下位レベルの★印のところです。
最終結果をFMEAフォーマットの「潜在的原因/故障のメカニズム」欄に記入します。
4-6 故障モードの発生度(O:Occurrence)の評価
潜在的原因や故障のメカニズムが起こり得る可能性を評価します。その評価を「設計FMEA・発生度(O)評価基準」に照らし合わせてランク付けします。メカニズムが起こりやすい故障モードに高いランクを付けます。それをFMEAフォーマットに記入します。
発生度(O)のランクが高い場合には、それを下げる方法がないかの検討が必要です。発生度(O)のランクを下げることは、「設計変更」を通して、原因やメカニズムを予防・管理することによってのみ可能です。
手順5.リスク分析
5-1 現行の設計での予防管理レベルと検出管理レベルの検討
現行の予防管理レベルの検討では、故障の原因・メカニズムや引き起こされる故障モードを予防し、それらの発生度を低減します。
現行の検出管理レベルの検討では、生産に引き渡す前に、分析的・物理的手法によって故障の原因・メカニズムや故障モードを検出します。
トラブルの発生度(O)のランクは、「現行の予防管理レベル」、「現行の検出管理レベル」を考慮して見直します。
5-2 故障モードの事前の検出度(D:Detection)の評価
「現行の予防管理レベル」と「現行の検出管理レベル」から、故障モードを検出できる度合のランク付けを、「設計FMEA・検出度(D)評価基準」に基づいて10段階で行います。検出しにくいものを高ランクにします。その結果をFMEAフォーマットに記入します。
検出度(D)のランクが高い場合には、それを下げる方法がないかの検討が必要です。検出度(D)のランクを下げることは、「予定された設計管理」を改善することによってのみ可能です。
5-3 故障モードの処置優先度(AP:Action Priority)の評価
以上の3つの評価基準より、故障モードの厳しさ(S)、発生度(O)、検出度(D)のランクが決定します。次に、この3つのランク結果より、起こり得るリスクの優先順位(重要度の高さ)を決めます。
リスク低減の改善処置(推奨処置)の優先度のことを、処置優先度(AP)と言います。処置優先度(AP)は、【厳しさ(S)>発生度(O)>検出度(D)】の基本思想をベースとしています。この思想を具現化し作成された、(S)(O)(D)の組み合わせ一覧表「設計/工程FMEA・処置優先度表(AP表)」により、自動的に一意的に決まります。
FMEA作成準備でご紹介した、設計/工程FMEA・処置優先度表(AP表)をご覧ください。
表中には、優先度のH:High(高)、M:Middle(中)、L:Low(低)が示されています。優先度の各レベルに対して必要な処置をとることが求められています。たとえば、組み合わせにより、「H(高)」に該当する場合は、推奨処置として、「予防管理または検出管理を改善するための行動を特定する、または、現在の管理が適切である理由を正当化する必要がある」とあります。
古いFMEAのリスク優先指数(RPN)から新しいFMEAの処置優先度(AP)への変更点
今回、改善処置の優先度を示す指標として、従来の「リスク優先指数」(RPN:Risk Priority Number=(S)×(O)×(D))から「処置優先度(AP)」に変更されました。
「リスク低減のためには、顧客への影響の厳しさ(厳しさ、S)が、もっとも重視されるべきである。算出方法((S)×(O)×(D))で求めたRPNでは、徹底しない可能性があるので、適切でない」というのが変更の理由のようです。
確かに、リスク優先指数(RPN)は3つの数値の掛け算なので、厳しさ(S)が高く重大な事故につながりやすくても、検出度(D)が著しく低ければ、RPNを低く評価して重大事故の可能性を見落としてしまう可能性があります。
ただ、企業によっては、「(S)を二乗して(O)を乗じ、Dを加える」といった計算式の工夫により、基本思想を徹底しているケースもあるようです。工夫しだいでは、従来のRPN方式でも、運用上は問題ないのかもしれません。また、故障モードがH(高)の場合、「状況により、かなりのリスク低減の処置をしないと、M(中)への改善が困難な場合がある」といった議論もあるようです。
いずれにしましても、APやRPNの値が高い場合は、「設計技術や管理技術に弱点がある」と言えます。
手順6.最適化
6-1 推奨処置
故障モードのランクを下げる推奨処置として、設計変更や特別管理、規格・規定等の変更を行います。設計変更を考慮した予防・是正処置が必要となります。
推奨処置が必要ない場合は、FMEAフォーマットの推奨処置の欄に「必要なし」と記入します。
6-2 責任者と完了予定日の決定
推奨処置がある場合には、推奨処置の実施責任者の個人名と完了予定日をFMEAフォーマットに記入します。実施責任者としては、設計部門を代表する人が望ましいです。完了予定日は、トップマネジメントや実施責任者と協議をして決めます。
6-3 処置の実施と評価
推奨処置が実施された後、実際の処置内容及び、実行日をFMEAフォーマットに記入します。
処置後のS/O/D再評価、及びAPの見直しを行います。推奨処置に「必要なし」と記入されている場合は、FMEAフォーマットに記入の必要はありません。
追加の処置が必要なら、「推奨処置」以降を繰り返し行います。常に継続的改善に焦点をあてるように心がけることが大切です。
手順7.文書化
設計FMEAの結果と結論を文書化し、関係者に周知徹底します。工程FMEAの担当者に引き継ぐことはもちろんのことです。この文書化されたものは、改善の経緯の把握に役立ちますので、FMEAフォーマットと同様にアーカイブとして保存しておくことが望まれます。
「工程FMEA」作成手順
以下、「工程FMEA」の作成手順をご説明いたします。既述の「設計FMEA作成手順」との共通部分は、紙面の都合上、多少割愛させていただき、理解に必要な部分を中心に記述させていただきたいと思います。
手順1.計画と準備
FMEA解析の対象製品及びその生産ラインを具体的に明確にします。
貴社は、「自転車(システム)」のサブシステムである「フレーム組立品」の開発計画中とします。図表、工程FMEA「機能分析・故障分析」をご欄下さい。工程FMEAの上位レベルには自転車の組立ラインが、下位にはプロセス&5Mがあります。
手順2.構造分析
FMEA解析の焦点となる「分析対象」を明確にします。方法は、設計FMEAと同様です。
手順3.機能分析
分析対象(フレーム組立品)、システム(自転車)、コンポーネント(部品)それぞれに対し、求められる機能や顧客などからの要求事項を明確にします。次の図表、工程FMEA「機能分析・故障分析」をご覧下さい。
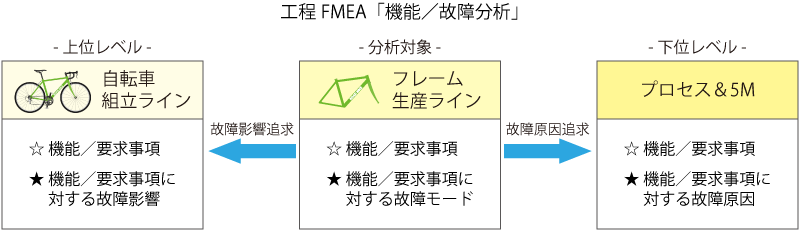
分析対象(フレーム生産ライン)、上位レベル(自転車組立ライン)、下位レベル(プロセス&5M)それぞれに対し、求められる機能や顧客などからの要求事項を明確にします。
手順4.故障分析
4-1 潜在的故障モードの検討
手順3で明確にした分析対象に対して、どのような故障モード(故障内容)が起こる可能性があるか(潜在的故障)、検討します。工程への要求事項/設計の意図に対する故障、不適合、次工程で引き起こされるであろう故障の原因など、すべての故障モードをリストアップします。
故障モードの例
製品の曲がり、亀裂、穴位置づれ、浅い穴、穴なし、取り扱い損傷、汚れなど
4-2 故障の潜在的影響の検討
次に、もしその故障が起こった時に、上位レベル(顧客、自転車組立ライン)にはどのような影響があるか、故障影響を検討します。リストアップされた故障モードから、自転車組立ライン、フレーム生産ラインやその次工程で気づく影響や安全の問題、法規制の逸脱をリストアップし、FMEAフォーマットに記入します。
故障の潜在的影響の例
製品の騒音、粗雑、誤作動、断続動作、不安定、臭い、漏れ、外観不良、環境への影響、ネジ留め不可、勘合不可、接続不可、搭載不可、装置に損傷を加える、作業者を危険にさらすなど
4-3 起こりうるトラブルの厳しさ(S:Severity)の評価
リストアップされた故障モードを、「工程FMEA・厳しさ(S)評価基準」に基づいてランク付けします。同時に、製品の安全性に対する問題や、法規制の逸脱がないかを確認します。
FMEAフォーマットにランクを記入します。
4-4 厳しさ(S)のクラス分け
通常、1つの故障モードに対して複数の故障影響がありますが、そのように影響の範囲が大きいものに、もっとも高い影響のランクを付けます。
クラス分けのランクは、例えば以下のようにします。
クラスA | 厳しさ(S)=9、10 |
---|---|
クラスB | 厳しさ(S)=5~8、発生度(O)=4~10 |
クラスC | その他 |
結果をFMEAフォーマットに記入します。厳しさ(S)のランクが高い場合には、設計変更またはプロセスの再設計によって、ランクを下げられるかどうかを検討します。
4-5 潜在的原因/故障のメカニズムの検討
次に、下位レベルにおける故障モードの潜在的原因やメカニズムを検討します。なお、1つの故障モードに対して、すべての故障の原因及びメカニズムを検討し、それらをFMEAフォーマットに記入します。
4-6 故障モードの発生度(O:Occurrence)の評価
潜在的原因や故障のメカニズムが起こり得る可能性を評価します。その評価を「工程FMEA・発生度(O)評価基準」と照らし合わせてランク付けします。メカニズムが起こりやすいものに高いランクを付けます。それをFMEAフォーマットに記入します。
発生度(O)のランクが高い場合には、それを下げる方法がないかの検討が必要です。発生度(O)のランクを下げることは、「設計変更」と「工程変更」を通して、故障モードの原因やメカニズムを予防・管理することによってのみ可能です。
手順5.リスク分析
5-1 現行の工程での予防管理レベルと検出管理レベルの評価と改善検討
現行の予防管理レベルの評価と改善検討では、故障の原因・メカニズムや引き起こされる故障モードを予防し、それらの発生度を低減します。
現行の検出管理レベルの評価と改善検討では、生産ラインのアラーム表示などのポカヨケや人為的なチェック体制など、検出能力を評価します。故障の原因・メカニズムや引き起こされる故障モードを検出し、是正処置を行います。
故障モードの発生度(O)のランクは、「現行の予防管理レベル」を考慮して見直します。
5-2 故障モードの事前の検出度(D:Detection)の評価
「現行の予防管理レベル」と「現行の検出管理レベル」から故障モードを検出できるランク付けを、「工程FMEA・検出度(D)評価基準」に基づいて行い、結果をFMEAフォーマットに記入します。検出しにくい故障モードは、高ランクに設定されます。
検出度(D)のランクが高い場合には、それを下げる方法がないかの検討が必要です。検出度(D)のランクを下げることは、予定された工程管理を改善することによってのみ可能です。
5-3 故障モードの処置優先度(AP:Action Priority)の評価
以上の3つの評価基準より、故障モードの厳しさ(S)、発生度(O)、検出度(D)のランクが決定します。この3つのランク結果より、起こり得るリスクの処置優先順位(AP)を、「設計/工程FMEA・処置優先度表(AP表)」に照らし合わせて決定します。
処置優先度(AP)の値は、設計FMEAと同様に、H:High(高)、M:Medium(中)、L:Low(低)の3段階で表されます。APの値が高いと、工程設計、工程管理に弱点があると判断できます。
手順6.最適化
6-1 推奨処置
ランクを下げる推奨処置として、工程変更や特別管理、規格・規定等の変更を行います。工程変更を考慮した予防・是正処置が必要となります。
推奨処置が必要ない場合は、FMEAフォーマットの推奨処置の欄に「必要なし」と記入します。
6-2 責任者と完了予定日の決定
推奨処置が必要な場合は、推奨処置の実施責任者の個人名と完了予定日をFMEAフォーマットに記入します。実施責任者としては、製造部門を代表する人が望ましいです。完了予定日は、トップマネジメントや実施責任者と協議をして決めます。
6-3 処置の実施と評価
推奨処置が実施された後、実際の処置内容及び、実行日をFMEAフォーマットに記入します。
処置後のS/O/D再評価、及びAPの見直しを行います。推奨処置に「必要なし」と記入されている場合は、FMEAフォーマットに記入の必要はありません。
追加の処置が必要なら、「推奨処置」以降を繰り返し行います。常に継続的改善に焦点をあてるように心がけることが大切です。
手順7.文書化およびフォローアップ
工程FMEAの結果と結論を文書化
工程FMEAの結果と結論を文書化し、関係者に周知徹底します。この文書化されたものを、設計FMEAの担当者にも周知することで、ノウハウの共有ができます。この文書化されたものは、改善の経緯を把握するためにも、アーカイブとして残しておくことが望まれます。
工程FMEAのフォローアップ
工程設計責任者により、工程FMEAのフォローアップを行います。フォローアップでは、推奨処置の実施責任者などの関係者に対し、次のことを重点的に確認します。
- すべての推奨処置が実施され、適切にFMEAフォーマットに記載されているか。
- 下記が実施されたことを、関係各所に問い合わせ、確認してまとめる。
- 工程設計事項の達成
- 技術図面・仕様書・工程フローの確認
- 組み立て・製造文書に反映
- QC工程表(コントロールプラン)及び作業指示書の確認
- 量産開始後を含めて、常に最新の技術水準を反映するように、工程FMEAを改訂し続けているか。
以上が、「設計FMEA」と「工程FMEA」の作成手順です。ぞれぞれの手順の詳細は若干異なるので、比較してみてください。
FMEAを知ったばかりの人にとっては、最初はなかなか馴染みにくいかとは思いますが、おおよそはご理解いただけたと思います。また経験した人にとっても、新たな気づきが得られたのであれば、誠に幸甚です。
個別開催のFMEAセミナーのお知らせ
チームコンサルティングIngIngでは、個別開催のFMEAセミナー(AIAG&VDA対応)基礎・導入編を承っています。
第一線でFMEAを構築してきた製造業改善コンサルタントが、FMEAについて知りたい企業様、FMEAの導入を検討している企業様に、FMEAの基礎知識や作成手順を、事例をまじえて丁寧に解説するセミナーです。
個別開催ですので、貴社のご事情や受講者のFMEAに対する知識量などに合わせて、セミナーの資料や内容をカスタマイズいたします。
FMEAをもっとしっかり理解納得して身に付け、皆さんの会社に導入してみたいと思われる方は、是非、セミナーをご利用ください。
個別開催のFMEAセミナー
詳細は、個別開催のFMEAセミナー(AIAG&VDA対応)基礎・導入編をご覧ください。
この記事の著者
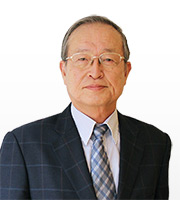
製造業改善コンサルタント
村上 豊 (Murakami Yutaka)
名古屋大学工学部、修士課程卒業後、トヨタ系列の電装を担う大手メーカーに30年間従事。製造部門のみならず、国内工場の工場長や英国の新工場立ち上げをも担当する。コンサルタントとして独立後、さまざまな製造業種の企業を支援し、5S活動の理論に基づいて工場の人材育成、生産、保全、品質、製造技術の改革に取り組む。人の能力を引き出し高めるマネジメントで、多くの製造工場の改善・改革、カルチャーづくり、理念経営を支援。