見える化とは
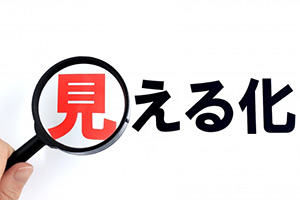
見える化とは、改善活動につながる問題点や重要点を見えるようにすることです。企業活動にはさまざまな問題点があり、改善を行う重要点があります。特に製造業の現場においては、見える化によって積極的な改善につなげることができます。
問題点が認識できれば、その問題点の本質や真の原因(真因)を追究するため、「5回のなぜ?」を行って因果関係を探ります。真の原因がわかれば、あとは適切な対策案を選定し実行します。すると、問題点を根本的に改善できます。そういった意味で、私は、見える化のことを「視認性の向上」と呼び、製造業改善コンサルティングのサービス提供時でも重視しています。
どんな達人でも、工場の現場を初めて歩いて見て回る場合、一見するだけでは異常はなかなか発見しづらいものです。見える化に取り組んでいる工場であったとしても、工場の現場に慣れている人から、説明を聞いて初めて問題や重要点がわかることが多いことが現状です。これでは、見える化に成功しているとは言えません。
以下、現場を正確に見る方法や、見える化の方法、見える化の課題などを述べたいと思います。
現場を正確に見る方法
見える化を行うためには、まず現場を正確に見る必要があります。
製造現場改善では、直接現場に行き、現物、現実(現象)を直接自分の5感をフルに活用し、全身で向き合います。5感は視覚、聴覚、嗅覚、味覚、触覚ですが、この中で視覚により得られる現場情報がもっとも多いように思います。ただし、他の感覚も劣ることなく重要で不可欠であること忘れてはなりません。
現場を正しく見るために、最初に視覚を使います。目で見て、平常時とは異なる様々なことを発見します。聴覚などの他の感覚でも問題が発見できます。例えば、異常な音が聞こえる場合には、問題点にさらに近づくことができます。ただ騒音が大きい現場ではなかなか気づくのは困難な場合が多いと思います。ですから、私が工場を巡回する場合は、まずは目で見る視覚を基本にしています。
「見る」という言葉は、普通にみることですが、しっかり対象に目をこらしてみることを、「視る」という言葉を使います。凝視の視です。さらに、目に見えない本質的なものをみる場合は「観る」を使います。この場合は前述の5感だけではなく、第6感ともいわれる「直観」が働くことが必要になります。
工場巡回ですべての異常点や問題に気づくことは、「見る・視る・観る」をフルに活用しても限界はあります。そこでもう1つの「みる」が登場します。「看る」です。
「看」の文字のつくりは、目という字の上に手があります。要するに、人やモノなどを見るときに、日差しが強く見えにくい場合など対象物をより見えやすくするために手をかざすことがあります。これと同じように、問題をしっかり見るために、余計なものに捕らわれないことです。この手をかざすことが、見える化の本質であると考えています。
見える化の方法5種類
具体的に、現場やオフィスなどで実際に用いられている見える化の手段として、私は経験的には以下の5つの方法があると考えています。簡単にポイントのみご説明します。
1. 強調法
文章や図表を見るだけや、現場に置いてあるモノを見るだけでは、かなりの関心がない限り、重要点が見過ごされることが多く、見える化としては失格です。そこで特に重要な部分を強調することで、より多くの人の注目を得るようにします。このような方法を「強調法」と呼んでいます。
具体的には、カラーのマーカーで重要な部分にアンダーラインを引いたり、色を付けたり、スタンドを立て注意喚起をするなど、この分類に入ります。工場や倉庫で、フォークリフトが移動する場所にアンダーラインが引いてあることが多いと思います。これも強調法の一種です。
2. 基準法
基準方とは、今の状態が正常化か異常かを判断する基準を設けることで、一見して識別できる方法です。よくある事例として、掲示されている管理グラフで、その状態が正常なのか異常なのかを示す限界線や目標線を記入する方法があります。
モノの置き場所やモノそのものが分かるよう明示する手法として、「表札」と「名札」と呼ぶものがあります。部品棚を例にすれば、部品ごとの置き場所を決め、それぞれの場所に「表札」をつけて部品名や番号などを記入します。一方、部品や部品を入れる箱には「名札」をつけ、同じ名称や番号などを記入します。
表札は家の表札と同じです。また、名札は小学生の名札と同じです。もし小学生が通学中に迷子になったとしても最後には自分の家にたどり着くことができます。「表札」と「名札」が一対一に対応しているからです。これがモノの「表示」の基本中の基本の考え方です。
基準法は、見える化の手法としては、工場の現場ではもっとも活用できるものです。もちろんオフィスの書類整理などでも有効です。
3. 暴露法
暴露法とは、隠れていたモノを、表に暴露することで、目に見えるようにする方法です。
例えば、不良品が見えないところに置いてあったのでは、せっかくの宝の山が台無しです。作業机などの台を用意して、不良品が発生したらその台に乗せ、人目にさらすことです。私は、この台のことを「さらし台」と呼んでいます。さらし台に乗せられた不良品は、当然人々の注目を浴びることになります。それが改善に結びつくのです。
暴露法には他に、外観の一部をカットして取り除き、内部の構造が見えるようにするカットサンプルを作る方法もあります。部品を外部から見ただけでは問題や不良が分かりにくい場合には、カットサンプルで内部を暴露させます。
4. 置換法
置換法は、空気の流れなどの直接目には見えないモノを、目にみえるモノに置き換えて観察する方法です。
例えば、実験室などで流体実験をする際、可視化実験と呼ばれるものが該当します。また、サーモラベルというものを、工場の配管や設備に貼る方法があります。配管や設備が一定以上の高温になると、ラベルが化学変化を生じ色が変わることを利用するもので、温度が上がったことを、直接手に触れなくても目で見て確認することができます。その他、酸性・アルカリ性を判定するリトマス試験紙も、この方法に該当します。
5. 表現法
表現法とは、目に見えない抽象的な概念を目に見える形で、具体的に表現する方法です。
これにはかなり多くの事例があります。まず、ビジョン(目標)などのビジュアル化(可視化)があります。目標が見えることで、さらにブラシュアップされていきます。仕事の流れを示す「フロー(連鎖)」、仕事の進捗を示す各種管理表など、多くのものがあります。
「5S改善の七つ道具」も表現法に該当します。5S改善の七つ道具とは、トヨタ生産方式をベースに私が開発した、製造業改善コンサルティングで用いる、次の7種類の見える化ツールです。
- 5Sチェックシート
- 管理グラフ
- 改善計画表
- なぜなぜシート
- 改善報告メモ
- エントリーシート
- PDCA報告シート
この7種類のツールを活用することで、見えないモノを見えるようにできます。「5S改善の七つ道具」を活用し、5S活動と併せて稼働率を大幅に高め、製品の品質改善に成功した事例があります。
製造業改善コンサルティングの5S活動については、こちらのページをご覧ください。
以上で「見える化」の5つの方法を説明しました。いずれも有効な方法で実証済みのものばかりですが、工場や物流倉庫の現場ではとくに「基準法」は必須です。また、オフィスや実験室では「表現法」を駆使せずして、高度な知恵や戦略はなかなか得られないと思っています。
これらの見える化の方法は、単独で使用するのではなく、数種類を組み合わせて導入すれば、さらに見える化の効果が発揮されることになります。
見える化の課題
見える化の課題として、IT化についてと、見える化が浸透しにくい理由について述べたいと思います。
IT化に潜む見えない化
パソコンでのデータや情報ももちろん、見える化の対象として私は含んでいます。IT化でパソコンが各自に行き渡るようになったので、データベースの導入で多くの情報が多くの人に共有化されてきています。業務上そのシステムをよく使う人にとってみれば情報が見える化されていますが、一般の多くの人にとってみれば、IT化によりかえって「見えない化」になってしまうことが、多くの職場で見かけるのではないでしょうか。
IT化されたデータを「デジタル」というのに対し、掲示物やモノや資料などを「アナログ」ということがあります。このアナログとデジタルの扱い方、組み合わせや融合の仕方でいかに知恵を出すかが、今後の「見える化」のポイントであると考えています。
見える化が浸透しにくい理由
現場の担当者は、正常か異常かはよくわかっています。だから、見える化の必要性はあまり感じないものです。
また、問題が慢性化していて、見える化の必要性を感じないこともあります。例えば、倉庫の入り口付近に、入荷した荷物が置かれ、倉庫の出し入れの邪魔になっていたとします。ところが、何年も前から同じことが繰り返されて慢性化し、工場で働く人は誰も気にならなくなっていることがあります。こういったことが積み重なり、工場の生産性や利益を圧迫していても、当事者としては理由が判らないままということがあります。
製造業改善コンサルティングで見える化を導入する場合、見える化により、自分にとって都合の悪いことが周りに知られてしまうため、むしろ見える化に消極的になることがよくあります。
その場合は、管理者による現場の指導力が問われますが、見える化に関心がない現場の管理者もたまにいて、見える化が浸透しにくいことがあります。これは、管理者自信が、見える化の必要性が十分に理解し納得できていないためと思われます。
現場の担当者にも管理者にも、見える化の狙いが何たるかの理解活動がどうしても必要となる所以です。
見える化を成功に導く製造業改善コンサルティング
製造業改善コンサルティングでは、現場に入って5S活動の一環として見える化の指導を行うことはもちろんですが、見える化を成功させて工場の生産性や利益を高めるために、プロジェクトメンバーの選出やリーダーの養成なども行っています。
見える化を導入したい会社、見える化が定着せずに困っている工場、見える化をしても目標が達成できない会社など、見える化のことなら製造業改善コンサルティングの導入をご検討ください。
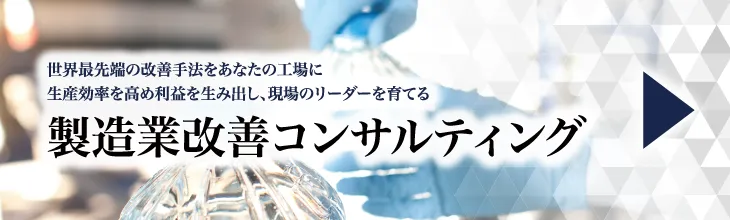