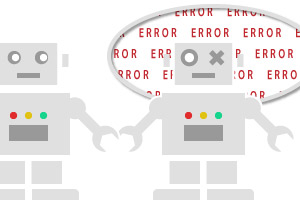
FMEAとは、「故障モード影響解析」(Failure Mode & Effects Analysis)の意味です。
最近の製造業では、FMEAという言葉が聞かれるようになりました。「FMEAのセミナーを開催してもらいたい」「FMEAを導入したい」というお客様が増えてきております。
このコラムでは、次の目次に沿って、FMEAとは何かを、わかりやすく解説いたします。
FMEA(故障モード影響解析)とは何か
製品設計上や、製造上のミスや不具合(以下、「故障モード」と呼びます)が、最悪の場合には、人身事故や死亡事故、あるいは法規制の逸脱などのトラブルにつながります。その対策として、FMEAがコアツールの1つとしてあります。
FMEAとは?
FMEAとは、わかりやすく述べると、小さなトラブルも含め、こういったトラブル発生を少しでも未然に防ぐための一連のリスクマネジメントシステムです。
製品のリスクについて、製品設計段階や工程設計段階で評価し、製品のリスクをできる限り無くしていく手法が規定されたものです。
新技術を用いた製品や新製品においては、部品の設計変更や工程変更などを行う場合に、FMEAをやり直して顧客に報告することになっている企業もあります。
AIAG&VDA FMEAとは?
もともとFMEAは、1960年代に、米国のNASAのアポロ計画で開発されたと言われています。有人ロケットのように、故障即死亡事故のような極端な業界で、故障ゼロを目指して開発されたものと思われます。
有人ロケットほどではありませんが、自動車業界も同じように、事故が人命にかかわる業界です。自動車の非営利団体である全米自動車産業協会(AIAG)は、「AIAG(米国)FMEAマニュアル」を開発し、その後長い間、自動車産業のFMEAのスタンダード的存在で、日本でも普及しました。
また、自動車大国であるドイツでもドイツ自動車工業会(VDA)が、「VDA-FMEA」を開発していました。
近年の自動車産業を取り巻くビジネス環境変化には、顧客ニーズの高まりによる競争の激しさ、法律による規制、自動運転などで、大変厳しいものがあります。それら変化への対応策として、「AIAG-FMEAマニュアル(米国)」と「VDA-FMEAマニュアル(ドイツ)」は、新しく「AIAG&VDA-FMEAハンドブック」として一本化され、現在に至っています。
この新しいFMEAは、従来我々が慣れ親しんできた「AIAG(米国)FMEAマニュアル」と相違点が多々あり、慣れるまでは多少時間がかかるであろうと言われています。主な変更点については、別コラム「FMEA作成手順を徹底解説」にて、ご紹介しています。
ISO9001でも取り入れられつつあるFMEA
いずれにしましても、現在では、FMEAが複雑なシステム構築あるいは運用時のリスクマネジメントとして、不可欠の手法となっているわけです。
品質マネジメントシステムには、製造業ではおなじみの「ISO9001」があります。2015年バージョン(ISO9001-2015)から「計画段階でのリスクへの取り組み」ということで、リスクマネジメントが具体的に追加されています(FMEAという言葉そのものは明示されていませんが)。
これにより、FMEAによるリスクマネジメントは、もはや自動車関連産業だけのものではなくなりました。
家電メーカー、物流、飲食など、未来予測でリスクを想定したいさまざまな業界で、ビジネス環境の複雑化や顧客要求の高度化、頻発するクレームなどへの確固とした対応が、それだけ厳しく求められているということでしょう。
FMEAの基本的考え方
リスクマネジメントには、環境アセスメントやデューデリジェンスなどがあります。FMEAは、ものづくりにおけるリスクマネジメントの手法の1つです。「リスクマネジメント」には、2つの機能があります。
1つは、故障(故障モードと呼ぶ)やそのリスク度合いを分析評価し、どれだけ大きなトラブルが市場で起こり得るかを事前に知る「故障の評価(リスクアセスメント)」です。
もう1つは、起こり得る故障やその原因に対して事前に処置(予防処置)することで、トラブルを回避する「リスク低減への推奨処置(リスクヘッジ)」です。
トラブルの評価(リスクアセスメント)
起こり得る故障の評価では、次の3つの評価基準(ランク)を設定します。
- 起こりうる故障の、顧客や社会への影響の「厳しさ(S:Severity)」
- 故障そのものの「発生度(O:Occurrence)」
- 故障やその原因の、事前の「検出度(D:Detection)」
評価基準は、1から10までの10段階で設定します。トラブルが厳しいもの、故障の発生度が高いもの、故障や原因の事前の検出が難しいものがランクアップしていきます。
3つの評価基準より、影響度(S)、発生度(O)、検出度(D)のランクが決定します。
リスク低減の改善処置(推奨処置)の優先度(処置優先度;AP=Action Priority)は【影響度(S)>発生度(O)>検出度(O)】の基本思想をベースとする、(S)、(O)、(D)の組み合わせ一覧表(「処置優先度表;AP表」と呼ぶ)により、自動的に決まります。
表中には、優先度のH(高)、M(中)、L(低)が示されており、優先度の各レベルに対して必要な処置をとることが求められています。
トラブルへの推奨処置(リスクヘッジ)
「処置優先度表(AP表)」から、故障モードを改善する優先度、H(高)、M(中)、L(低)が決まります。もちろんH(高)に対応する故障モードから、改善していくことになります。推奨処置を決め、実行していくことになります。
従来は、この処置優先度(AP)ではなく、リスク優先数(RPN=Risk Priority Number)が使われていました。新しいFMEAでは、RPNは使用されなくなりました。この変更理由などについては、次回のコラム「FMEA作成手順を徹底解説」にてご説明したいと思います。
FMEAの上述の考え方は、ここでは、工業製品づくりの「製品設計」、「製造工程」に適用します。それぞれ、「設計FMEA」、「(製造)工程FMEA」と呼んでいます。つまり、設計FMEAとは製品設計におけるFMEAのこと、工程FMEAとは製造工程におけるFMEAのことです。
ちなみに、設計FMEAのことをDesign FMEAの略で「D-FMEA」、工程FMEAのことをProcess FMEAの略で「P-FMEA」と呼ばれることもあります。
FMEAが導入されている業界
実際のFMEAが導入されている業界は、自動車業界、機械部品業界のみならず、食品業界(HACCP)等を含む多くのものづくり業界、その他、石油化学業界、電子部品・半導体業界、医薬・医療機器業界など、幅広く導入されています。
故障によって生命の危険がある業界や、多くの人に迷惑をかけてしまう業界など、故障が許されない業界にはFMEAの導入はとても有効です。
可能性として、FMEAの考え方はソフトウェア開発にも応用できると思います。
FMEA適用のメリット
FMEA適用のメリットは、大きなトラブルが発生する前の予防処置により、トラブル発生を回避し、発生に伴う多くの費用を軽減できます。
FMEAの作成が事前に完了していれば、その後の設計変更や工程変更を容易に、かつ最小限の費用で実施できます。
場合によっては、生命の危険を回避できることにもつながります。
品質保証制度での重要な役割
製造業の企業が、何か新製品を開発する場合には、全社関連部門で総力をあげて、品質目標達成に向けた活動をしていきますが、その際の基盤となるシステムが「品質保証制度」です。
新製品の立ち上げは、基本的には以下の流れになります。
「企画」→「製品設計」→「試作」→「工程設計」→「量産試作」→「量産」
この流れに、FMEAを加えると、次のようになります。
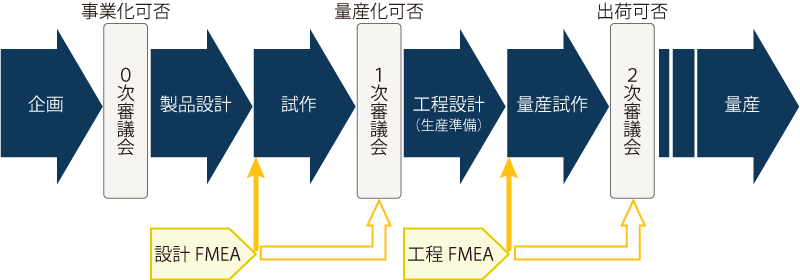
この流れを支える基盤システム「品質保証制度」に「FMEA」がリンクしているのです。以下、この流れにおけるFMEAの関わりをご紹介いたします。
「製品設計」の前段階【企画段階(0次審議会)】
0次審議会は、製品設計に入る前のデザイン・レビューのことです。製品企画案が固まり、事業性を評価し、具体的に設計作業に入るか否かを決定します。
「試作」の前段階【設計FMEA】
設計FMEAを作成します。1次審議会に諮り、承認を得ます。
「工程設計」の前段階【設計仕様固め段階(1次審議会)】
設計仕様が固まり、設備等の生産準備に入るか否かを決定します。
「量産試作」の前段階【工程FMEA】
工程FMEAを作成します。2次審議会に諮り、承認を得ます。
「量産」の前段階【量産試作段階(2次審議会)】
量産試作を終え、所定の品質やその他の目標達成の目途が得られると、出荷するか否かを決定します。
設計変更を行う場合は、設計FMEAを改訂します。工程に変更箇所がある場合は、工程FMEAを改訂します。
FMEA作成の流れ
設計FMEAや工程FMEAを作成する手順は、次のように「7つのStep」を踏みます。
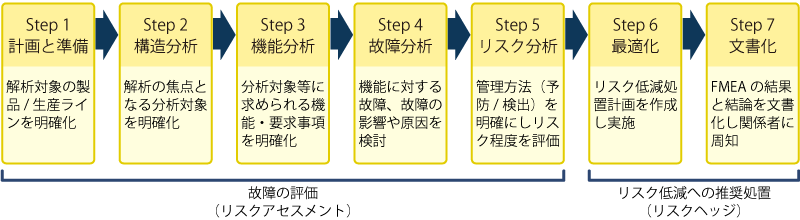
「FMEAの基本的考え方」で述べた、「故障の評価(リスクアセスメント)」が、Step1からStep5に該当します。「リスク低減への推奨処置(リスクヘッジ)」が、Step6とStep7に該当します。
一般には、先に設計FMEAを作成します。設計段階では、トラブルが出ないように設計をしているため、顧客要求事項や特殊事項などを合わせた申し送り事があるはずです。その指摘を配慮して、工程FMEAを作成します。
設計FMEAや工程FMEAを作成するとき、評価スコアや所要事項を記入できる専用のフォーマットを使用します。次の図は、FMEAフォーマットのサンプルです。
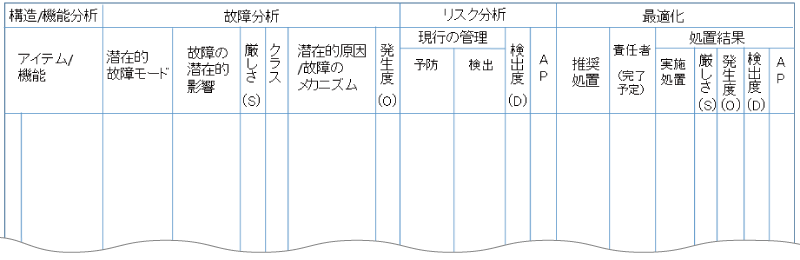
設計FMEAや工程FMEAを作成する手順「7つのStep」を簡単に説明すると、次のようになります。
故障の評価(リスクアセスメント)
Step1:計画と準備
解析対象の製品/プロセス(工程)を明確化します。
Step2:構造分析
解析の焦点となる分析対象を明確化します。
Step3:機能分析
分析対象に求められる機能・要求事項を明確化します。
Step4:故障分析
機能・要求事項に関する故障、故障の影響(S)、故障の原因を検討します。
Step5:リスク分析
管理方法(予防管理/検出管理)を明確にし、リスク程度を評価します(S/O/D→AP)。
リスク低減への推奨処置(リスクヘッジ)
Step6:最適化
リスク低減処置計画を作成し、実施します。(見直し後のS/O/D→AP)
STEP7:文書化
FMEAの結果と結論を文書化し、関係者に周知・徹底します。
設計FMEAと工程FMEAでは、評価基準や作業内容が異なります。設計FMEAや工程FMEAの作成手順の詳細については、「FMEA作成手順を徹底解説」をご覧ください。
最後に
以上、FMEAについて、定義、基本的な考え方、用途やメリットについてご説明してきました。また、工業製品を中心に的を絞り、FMEAの2本柱である、「設計FMEA」、「工程FMEA」の作成手順(7つのStep)をご説明しました。
尚、既述の近年の改訂で、新たに追加された規格、「FMEA-MSR」があります。「電子制御システム」を対象としており、設計FMEAを補完するものです。今回、ご説明は割愛させていただきましたが、また別の機会で是非ご紹介したいと思っています。
FMEAについて、初めての人にとっては、最初はなかなか馴染みにくいかとは思いますが、おおよそはご理解いただけたと思います。また経験した人にとっても、新たな気づきが得られたのであれば、誠に幸甚です。
FMEAは、工業製品のみならず、食品など製造業全体のものづくりのリスクマネジメントとして、もっとも優れたものの1つであると考えています。
先述しましたが、FMEAは、NASAのアポロ計画時に開発されたものです。ものづくりのみではなく、高度で複雑なシステムや仕組みづくり分野でも十分活用できるものと思います。そこで、宇宙関連の事例を最後に取り上げたいと思います。多くの教訓が得られると思うからです。
小惑星探査機・はやぶさ、奇跡の帰還
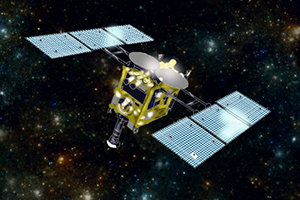
小惑星探査機「はやぶさ」のプロジェクトは、「3億キロ彼方の小惑星イトカワまで航行し、1秒ほどの着陸と離陸の間にサンプルを採取し、地球に帰還する」というものです。
小惑星イトカワの全長は535メートル。地球からの惑星間航行は、「東京から地球を半周して、ブラジルのサンパウロの空を飛ぶ体長5ミリの虫に弾丸を命中させるような精度が要求される」という超難易度が高いものでした。
当時、プロジェクトメンバーがNASAとの研究会の席上で、「日本はイオンエンジンを使って小惑星サンプルリターンをやります」と宣言したとき、「FMEA産みの親」ともいえるNASAが、あまりのハイリスクのため、結果的には共同参画しなかったようです。「はやぶさ」は、小惑星サンプルリターンの技術を実証するための工学実験探査機でした。
以下の5つのミッションは、いずれも世界初の試みだったのです。この内容から、超ハイリスクであることが分かります。
ご参考に項目とポイントのみご説明します。(『全員経営』野中郁次郎/勝見明著(日本経済新聞出版)より引用)
(1) イオンエンジンによる惑星間航行
推進剤のキセノンを電気分解し、できたプラスイオンを吹き出すのがイオンエンジンです。推進力は弱いが、燃費がよい、ということで、プロジェクトの成否の鍵を握っていました。
(2) 宇宙の彼方での自律誘導航法
地球とイトカワ間の通信は往復約40分! 地球から何か命令を出しても、そのレスポンスに40分かかることを意味します。
そのため、はやぶさは自立誘導して、着陸と離陸の間(1秒間)にサンプルを採取します。
(3) 微小重力下でのサンプル採取
探査機に取り付けられたサンプルホーンという筒状装置の先端が着地すると、中から弾丸が発射されます。表面を砕いて資料を採取する方法が考えられました。
(4) イオンエンジンを使用した地球スイングバイ
スイングバイとは、衛星が星の近くを通過するときに、その星の重力を利用して加速をつける方法です。
はやぶさは、打ち上げられた後、太陽の周りを一周して、地球スイングバイをするために再び地球に接近します。そのときに、イトカワの方向に向かうために、正確な軌道修正が求められました。
このときに、はやぶさは、世界で初めて「スイングバイとイオンエンジン推進の組み合わせ」を行い、成功させました。
(5) カプセルによる大気圏再突入
資料採取容器を入れたカプセルを大気圏に再突入させる際の速度は、スペースシャトルを上回ります。そこで超高熱に耐える技術が必要とされました。
プロジェクトでは当然あらゆるリスクマネジメントを追求したはずです。想定され得るあらゆる故障モードを、メンバー全員で徹底的に検証していると思います。
さらには、少しでもリスクを削減するため、全員寝食を惜しんで、改善をしていることが推察されます。
入念にリスクマネジメントが行われたにもかかわらず、はやぶさ打ち上げ後は、想定外のトラブルが続出したと言われています。しかし、プロジェクトメンバー全員で、困難ではあるが魅力的な目標を共有していました。
一人ひとりが強い当事者意識を持ち、目標達成に向け智恵を出し合い改善していきました。最後は、イトカワのサンプルを採取して、はやぶさは地球に帰還することができたのです。
NASAでは持ちえない、日本ならではの強みが遺憾なく発揮されたと言えるでしょう。
FMEAは強力なリスクマネジメントの手法です。しかし、同時に、数々の想定外のトラブルにもめげない、目標達成への熱い思いが大切であることを物語っているといえるでしょう。
当社の品質管理コンサルティングでは、コンサルティングが進んだ企業様では、設計FMEAや工程FMEAの実施と作成をご支援しています。これからFMEAを導入したいとお考えの企業様は、お気軽にご相談ください。
FMEAセミナーのお知らせ
チームコンサルティングIngIngでは、個別開催のFMEAセミナー(AIAG&VDA対応)基礎・導入編を承っています。
製造業改善コンサルタントである私が、第一線でFMEAを構築してきたノウハウをお教えします。FMEAについて知りたい企業様、FMEAの導入を検討している企業様に、丁寧に解説するセミナーです。
個別開催のFMEAセミナーにご興味のある方は、ぜひ個別開催のFMEAセミナー(AIAG&VDA対応)基礎・導入編をご覧ください。
個別開催のFMEAセミナー
詳細は、個別開催のFMEAセミナー(AIAG&VDA対応)基礎・導入編をご覧ください。
この記事の著者
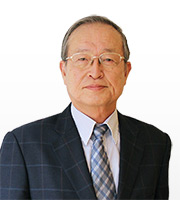
製造業改善コンサルタント
村上 豊 (Murakami Yutaka)
名古屋大学工学部、修士課程卒業後、トヨタ系列の電装を担う大手メーカーに30年間従事。製造部門のみならず、国内工場の工場長や英国の新工場立ち上げをも担当する。コンサルタントとして独立後、さまざまな製造業種の企業を支援し、5S活動の理論に基づいて工場の人材育成、生産、保全、品質、製造技術の改革に取り組む。人の能力を引き出し高めるマネジメントで、多くの製造工場の改善・改革、カルチャーづくり、理念経営を支援。